Saturday was quite possibly one of the longest days working on our house. Or maybe working in an attic during the 105 heat index made it feel even worse. The day started off well (and cool) enough, as our electrician Fred showed up as promised bright and early. After walking through the details with Jay, he put together a shopping list of a few extra items that Jay had not already picked up.
While Jay ran to Lowes, Fred started drilling through walls studs, sawing 1/2" metal conduit with a cool cordless bandsaw (which Jay promptly nicknamed "The Green Machine"), and contorting metal conduit into all kinds of funky shapes. Smartly, Fred started working on the non-A/C side of the attic first (the side that faces West and will be the master bedroom). He had most of the bedroom complete by the time Jay returned.
In the past year since Fred wired our basement, Jay had tried a few times (mostly unsuccessfully) to work with conduit and the pipe bender he has. Now, Jay was a willing apprentice as Fred tried to teach him some of the tricks of measuring and bending conduit. With a little help, it actually wasn't too bad. Jay ended up doing the stairs, half of the hallway lighting and smoke detectors, and half of the spare bedroom before the day was done.Granted, that is only about 15% of the work and Fred needed help on some things a lot, but still, not too bad for an amateur.
By 5 o'clock we started moving slow as the heat sunk in and the A/C struggled to keep up. But Fred was determined at that point to get all the piping done before he left for the day. We pressed on, figured out a way to route the conduit down to the main circuit panel in what's termed the "homerun". I thought Fred kept referring to the Cubs spanking the Cards until I figured that out. Additionally, the centrally-wired smoke detectors will need to be wired into existing smoke detectors in the basement, so that required another pipe coming downstairs as well.
Then we determined that we were out of conduit. We'd already gone through about 450 feet of pipe(!) but needed another 40 more to finish the spare bedroom. Mostly this was because an earlier pipe Jay had run before the floor was completed turned out to be unusable.
After thinking this spelled the end of the day, Fred said no way. He was not leaving when we were so close to finishing. Maybe he's just a glutton for punishment. Or was trying to avoid his visiting in-laws. At any rate, when the work was finally done it was pretty much 8:30. Subtracting the half hour for lunch, that was 13 hours of work! Wow.
Fred says pulling the wires should only take 1/2 day though. Not quite clear if that means a normal 7.5 hour day or a true half day (4-5 hours) though. At any rate, he'll be coming out to finish the job and hook up some temporary outlets and lighting for us. Then we'll actually have power (or Lectre) and be able to call for the rough inspection. Woot!
Sunday, July 30, 2006
Piping for 13 hours
Posted by
jay
at
9:27 AM
0
comments
Labels: electricity, second floor, wiring
Thursday, July 27, 2006
The 'Lectre is coming!
When my cousin Chase was around 5 years old, he had a tendancy to give special powers to his toys. The action figures invariably had the ability to "Lectre" any villians. I thought this was some wierd invention he came up with, or maybe something was lost in translation due to the foreign culture (he's from the South). After all, he later told me how he wanted to be a firetruck when he grew up. But after several weeks, it finally dawned on me that this was his shorthand for "Electricity."
We at HumphreyHouse are looking forward to this weekend, when our electrician Fred will be coming over to Lectre the upstairs. While it is doubtful he will complete everything, hopefully we will at least get some decent lights up there, and be able to walk up and down the stairs without tripping over extension cords anymore.
Maybe Fred can even teach Jay how to measure and bend conduit on his own for the future, too! We can only hope that our anticipated 99 degree highs (with 80% humidity) can be tempered with the extra window A/C unit and temporary HVAC we've routed from downstairs. Or hopefully at least enough to avoid dehydration.
Posted by
jay
at
12:47 PM
2
comments
Labels: electricity, piping
Monday, July 24, 2006
How it feels to live in HumphreyHouse
Over the past weekend, we saw many friends and family members, who invariabily asked "How's the house coming?"
Well, sometimes it just gets overwhelming, so much so that it can almost be difficult to express in words. That is, until you find a cartoon that sums it up perfectly:
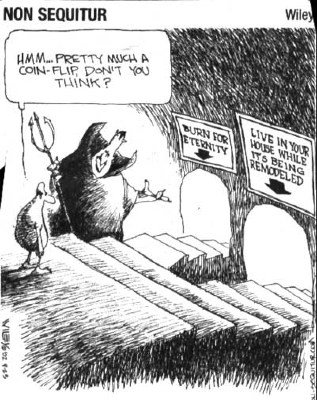
Posted by
jay
at
1:09 PM
2
comments
Tuesday, July 18, 2006
A skeleton in the attic
Gramma's ghost has given way to a skeleton, as sidewalls, knee walls, and ceilings emerge upstairs.I think this is one of my favorite parts of the whole construction process. For the first time, you start to see how the plans and designs you drew up (years ago) physically take shape. No more 1/4" = 1 foot scale; this is the real thing. Three dimensions, baby!
And it allows you to come up with other ideas. Such as pocket doors to allow more space (and light) into what will be a somewhat narrow laundry room. Or laying out and framing openings for future built-ins, such as two dresser drawers in what will be the master bedroom.Many of the interior walls are being constructed by our contractor, but Kenny and Brian came up to lose weight during Chicago's massive heat wave last weekend by working in our attic with Jay. Actually, Brian raised the ceiling framing in the master bedroom, and Kenny helped construct the knee walls and insulate the under-eave areas.
Getting the materials upstairs proved to be fun as Mark briefly stopped by at the perfect time to help Ken and Brian toss boards up through the window. This assembly line was so much easier than carrying things through the kitchen and up the stairs. Wish Mark had thought of this sooner! ;-)
Anyway, thanks to Brian and Kenny's help, we got through the long weekend, and we are nearly complete with the framing for upstairs. We're planning on having the electrician come next weekend, and it all needs to be in place by then.
Posted by
jay
at
5:36 PM
3
comments
Labels: bedroom, brian, built ins, framing, kenny, many hands, mark, second floor
Wednesday, July 12, 2006
Living Room Renaissance
Last weekend, Jen's dad came up to lend a hand with a variety of tasks. While our contractors worked on completing the subflooring upstairs, Kenny and Jay worked on tracing the path of the living room light fixture.
Backstory: After moving in, we noticed an unused electrical box with a cover on it in the center of the ceiling. Not too surprising, right? Well, the surprise was that there was no switch to be found on any of the walls. Even shining a flashlight up along the wall to look for signs of obvious patching yielded no clues (although it did show us that the arches were added after the walls were built - probably in the 50's when that was a big remodeling movement).
While we had guessed where the switch might be, we never really knew until the floor upstairs was removed. Jay was then able to trace the conduit down to one joist bay, in the wall between the living room and the foyer. We also found that this light was one of the three gas-electric lights in the house, along with the Kit and DR. How cool! (The gas lines had been removed in the basement long ago). Now we knew where the cable led to, so we just needed to find the old switch box that some Previous Owner (PO) decided to cover up.
However, it turned out that our detective work was not quite finished. To locate the box, we drilled test holes at the right height for a switch box. Didn't find anything. One of us went upstairs, shook the electrical conduit like mad while the other tried to "hear" if the box had just been pushed into the wall and was floating around in there. Nothing.
We began to question ourselves. If some PO had removed the light, there must have been a good reason, right? I mean, you don't just go about removing lights from your house, do you? Was the light leaking gas (when it was gas-powered light) or something? Was the electric line broken somewhere? Were the wires even properly taped or capped off?
Finally, we decided to start cutting a hole about 4 feet off the ground in the wall. But from the backside (our entry closet) - so at least the living room side would appear okay. Still nothing. Where could it be? We peeked upwards from the hole and were shocked to see the electrical box - about a foot up! This means that the original switch was nearly 5 feet off the ground! No wonder we found no trace of it. We can only assume the Original Owner must have wanted this for some reason. Maybe so kids wouldn't play with the gas-lights or something. Or maybe they just ran out of conduit.Anyway, we eventually got a new box installed at a normal height, tested the circuitry (it was all in good shape), patched our holes, and attached a vintage-looking light fixture that Jen and I had found at a demolotion sale last year. And guess what? It fits the style of the room perfectly! Which leads me to wonder, why did some PO remove the wall switch?
Posted by
jay
at
6:55 PM
3
comments
Labels: electricity, living room, restoration
Thursday, July 06, 2006
Plumbing, Take 2
Well, I now feel like I could act as a plumbing consultant (at least for OP village code) to ensure that everything comes into compliance. Educational experts always say that the best way to learn is through failure. Well, that's what happened to us, along with a whole lot of extra work. Good thing we had the extra time from a holiday weekend.We started off by demolishing (yet another) wall in our kitchen to expose the cast iron pipe. The old vertical stack needed to be replaced since we were cutting out a section of it below. That was a bear of a job, but a special chain pipe cutter that John brought made the job easier. Unfortunately, in order to remove the old stack, we also had to replace the 1st floor bath toilet drain which was molded into the old cast iron pipe. Of course, in order to fully reach that, we had to drop one of our HVAC supply ducts in the basement. Then we were finally able to start chiseling out the old drain, which was embedded in the 3-4 inches of concrete "subflooring" under our first floor bathroom. It's hard to convey just how hard this whole process was in words, and, sadly I did not take any photos before the cast iron was removed. But the whole process took the better part of Saturday, if that gives you any idea. By the time the pipe was out, we had just enough time to run the new PVC pipe from the basement upstairs, and reconnect our toilet.
As you can see, things started to get messy and complicated in the basement utility room with all the PVC pipes from upstairs connecting in to the stack.
After failing our inspection last week, we learned we could purchase a copy of local building code amendments for "a nominal fee". Turns out that it is only $5.00! Well worth the investment, and something I wish we'd known of earlier. It will definitely come in handy as it contains the amendments for ALL building codes, not just plumbing.So on Monday, we moved on upstairs and rerouted all of our "improper" venting in the attic. We did this early in the morning (8am!), which fortunately turned out to be relatively cool up in the attic while it was raining. By the time the showers passes, it was noon, and we had completed everything except pushing the pipe through the roof (finished later that afternoon).
Then it was down to the basement, where we were able to devise a monstrous maze of piping. (photo coming soon) Why so complicated? In order to make sure every little nit-picky thing that we could be failed for was taken care of so there was no chance of failing the inspection again.
And guess what, when the inspector came at 10:30 this morning, he was very pleased to see everything was so well done and completed correctly. So, now we can continue with flooring and framing!
Posted by
jay
at
11:30 AM
7
comments
Labels: cast iron pipe, inspectors, john, plumbing, pvc